So why travel there, you ask… besides being a nice small town, with beautiful surroundings, it is the place where Gripping Beast has it’s HQ, well ok, it’s only location, Beast Tower as it’s called and
ruled by it’s fair and wise lord, Lord S. I am fortuned to know this great warming persona and got to visit there. Read on to find out everything about “where the magic happens”!
Walk through snowy Evesham to get to my “old school hotel”, which was quite nice indeed!
GRIPPING BEAST
After a very British breakfast I took a taxi and arrived to Beast Tower… where Lord S., whom nowadays looks strikingly like Santa, welcomed me and we started chatting about the company history, which is quite an interesting story already in itself!
Andy got involved with the company, while still working on his previous profession in aviation industry.
After making himself redundant there, he could take a deep dive and he bought the company. One of the original owners still sculpts for GB.
GB has moved around England during it’s history, but has now settled in the quiet Evesham, where they have recently expanded their facilities and are hiring more staff.
I was very happy to hear this, as I know, that both the silly Brexit and then COVID-19 has really hurt the industry and somewhat (specially the oh so stupid Brexit) still does.
In order to fight the increased material and shipping costs, GB is now preparing to start SIO Casting their metal ranges in resin. This will be launched as an alternative for the metal,
and it will be cheaper in terms of retail price and shipping cost, compared to metal.
IMHO these resin casts look at least as good as the metal ones! They just need to sort some production issues with this new material and they should be up and running soon!

But then it was time to immerse myself into the real thing - making miniatures!
In the pictures below you can see the Siocast machine, used for the resin casting, raw materials and the machine for making the moulds (silicone).



Making metal miniatures
All GB miniatures are sculpted by contracted (aka not employed) sculptors. They are still made in the “old way”, that is to say computer design is not (yet) involved.
In a nut shell steps to produce our toy soldiers are as follows:
1. Sculptor is given an order to produce the master design models, vision of what is wanted is communicated
2. Typically starting from a metal dolly, sculptor sculpts the master in it’s actual size with green stuff. Pre made metal items, like weapons are used to speed up the process
3. Using the master design a master mould is made, below the master mould for this years UK Saga Grand Melee miniature
4. Production moulds are made from first metal casts from the master. Typically a production mould produces several miniatures
5. Miniatures are cast, this takes a steady hand and a steady pour
6. Miniatures are removed from the mould, clipped clean and checked for quality
7. Miniatures are organised to sets to be sold and stored for picking as demanded
Machine for the mould making. Silicone is melted and then made solid again, formulating a detailed mould.


Library of production moulds. Master moulds are kept in a different location, they stand as the proof of copyright and could be used to rebuild the production, should a disaster happen at production facility.
Casting
The liquid metal reaches a temperature of almost 300 C. In the melting pot below, failed casts are recycled, hence the stuff floating on top of it
Here you can see how the metal has moved to fill the mould slots, as said fluent and steady pour is needed.
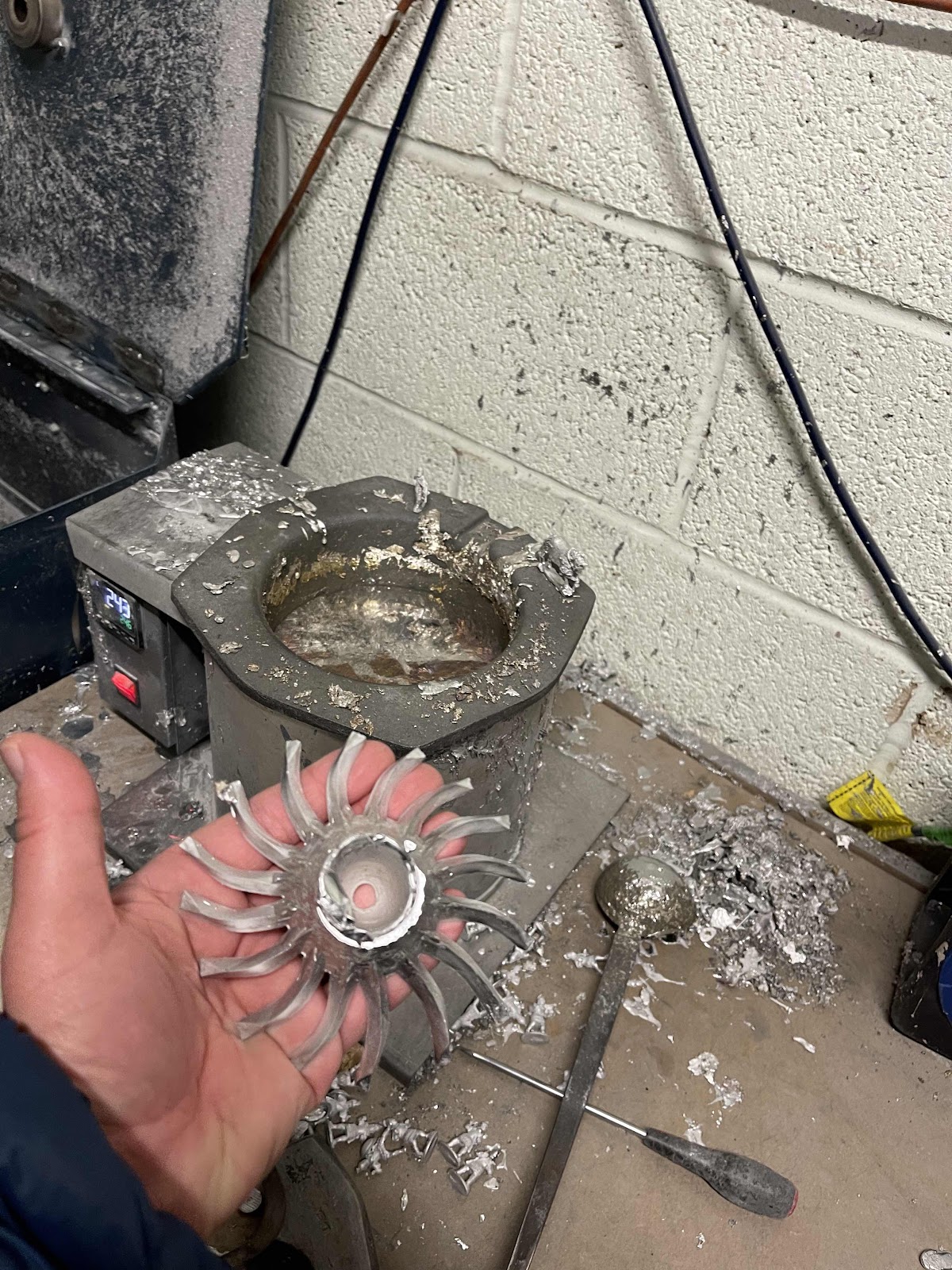
Clipping and quality control
Packing. Blisters are only used for retail. North Star takes care of distributing GB miniatures to UK resellers.

Sorted weapons and shields. Spears are not typically cast, as they are difficult to get right (hence the wire spears often included).


One of the staff members, Darren, also paints some of the miniatures needed for photo shoots etc.
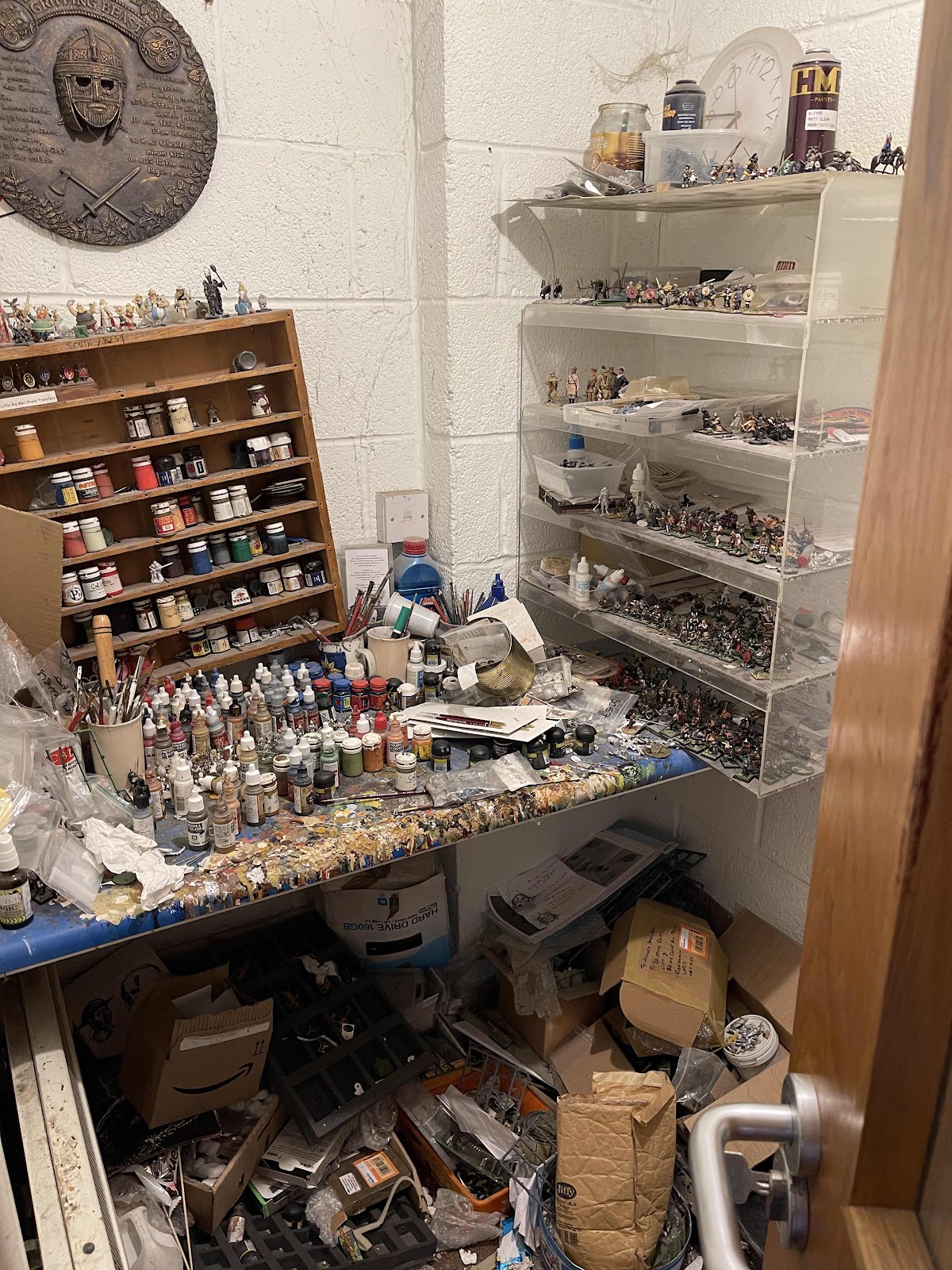
Some of their models on display in their gaming area.

Some of their models on display in their gaming area.
The style of different sculptors can be seen in the models.

Larger Jugula miniatures

Blisters for orders are organized down there
One mustn’t mess with the packing department!

Making plastic sets
Making plastic miniatures is quite different from making metals. Sculptor makes the original master model 3-ups
as much larger versions. Then the model design is scaled down with a mystical tool (I already forgot it’s name). One must take into consideration, that the cast frame needs to come neatly off the mould.
Renedra in UK makes the plastic moulds and produces the plastic miniatures for Gripping Beast. I really love their plastic sets, they
are one of the best plastic sets in the market.

Here you can see the size difference of original 3-ups and the eventual plastic miniatures.

It was truly a privilege to meet with all of the nice GB staff and learn about origins of our dearly loved toy soldiers!

Thank you Lord S. for your time and hospitality! Until next time!
Ei kommentteja:
Lähetä kommentti
Huomaa: vain tämän blogin jäsen voi lisätä kommentin.